有时候真觉得注塑成型是一门既科学又艺术的活儿。特别是遇到TPE这种弹性体材料,不少人以为只要温度、压力、速度调好了就万事大吉。可在实际生产中,哪怕你把温度和压力都调到“教科书水平”,只要背压设置不当,照样会出毛病。在我这些年跑工厂调机、跟线的经历里,关于TPE注塑,背压这个参数可算是最容易被忽视,却又最容易出幺蛾子的工艺条件。
文章目录
TPE注塑里背压到底干嘛用?
先别嫌基础,这点其实很多调机师傅都没讲清楚。
简单来说,背压是螺杆在回料(计量)时所需要克服的阻力压力。它就像一个看不见的“刹车”,让螺杆在后退时多花点力气,挤压熔体,使:
熔体密度更均匀
熔体里的气体、挥发物更容易被排出
熔体温度更均匀(因为被多次剪切)
如果背压太小,螺杆轻轻松松就退回去,料还没被好好混合;如果背压太大,又会带来剪切过热、分解、填充过度等问题。
背压的大小,直接决定了哪些TPE制品问题?
在车间现场,TPE产品会出哪些麻烦?总结下来,和背压关系特别大的主要有以下几种:
问题现象 | 背压过小时容易出现 | 背压过大时容易出现 |
---|---|---|
产品表面有气纹 | ✔️ | |
产品缩水塌陷 | ✔️ | |
制品尺寸波动 | ✔️ | |
料容易分解、变色 | ✔️ | |
螺杆回料慢、过剪切 | ✔️ |
我遇到不少客户,材料都用得很贵了,还在纠结射速、模温,结果背压一直在3~5 bar,调到10 bar后很多问题瞬间解决。
背压大小对TPE性能的具体影响
1. 对制品致密度和缩水的影响
背压太低,料就像“松散的棉花”,充模后冷却收缩更多,自然容易缩水。适当提高背压能让料更密实,减少缩水、凹陷。
2. 对制品表观(气纹、流痕)的影响
TPE常常比较粘稠,如果背压太小,螺杆回料快,气体来不及排出,容易在产品表面形成银纹、气纹。稍微提高背压,能把气体更充分排出。
3. 对熔体温度均匀性的影响
螺杆在回料时会对熔体产生剪切热,适当背压可以增强这种混炼,料温更均匀,不会出现一部分太热一部分还冷,导致充模不稳定。
4. 对分解与变色的影响
当然,凡事过犹不及。如果背压调太大,螺杆在回料过程中长时间高剪切,TPE容易过热甚至发生热分解,导致制品黄变、机械性能下降。
我是怎么实际设定TPE背压的?
在我的调机经验里,不同的TPE要对应不同的背压范围。比如:
TPE类型 | 推荐背压范围 | 特点与原因 |
---|---|---|
SEBS类TPE | 8~15 bar | 粘度较低,主要防止气纹 |
TPU | 5~12 bar | 易水解分解,不宜太高 |
TPO | 10~20 bar | 粘度较高,需要适当高背压防缩水 |
TPEE | 8~18 bar | 硬度高流动差,靠背压均化熔体 |
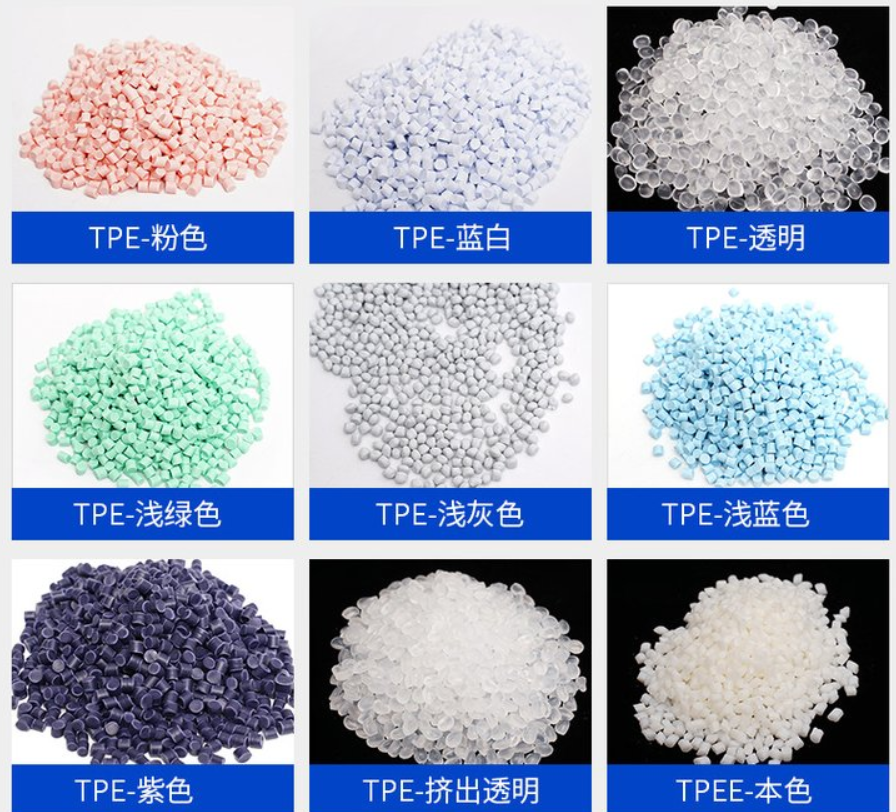
说点背压调节的小细节
观察螺杆回料时间
一般螺杆回料时间应该在射胶时间的1.5倍左右(粗参考)。如果回料太快可能背压太低,太慢又说明背压过高。
看回料声音
有经验的机台师傅都爱趴机器旁边听声音。正常的背压回料会有稳定的“嘶——嘶——”声音;背压太小容易“扑扑”,太大则“呜呜”发闷。
注意脱模收缩情况
同样一副模具,背压从5 bar提高到12 bar后,TPE制品脱模收缩一般会变小。
避免过高背压导致温度升高
尤其是TPU类,过剪切容易黄变。多留心料筒排气口有没有轻微白烟或焦味。
我的几个实用小结论
为了少走弯路,我自己一般都这样做:
初次试模从中值背压开始(比如12 bar),然后分阶段加2 bar测试。
每次调节后,至少打5~10模,观察制品尺寸、表观再做结论。
尽量少用极端背压解决问题,比如动辄20 bar以上,多半会带来别的问题。
说白了,背压就像给料加个“阻尼”,既能帮你把料搅匀、排气,也容易过头,所以要多观察螺杆回料状态和制品细节。
相关问答
Q:TPE注塑背压可以直接调到最大,保证料密实吗?
千万别。背压过大除了料筒容易过热,还会加速螺杆与料筒的磨损,长期反而得不偿失。
Q:背压会影响注塑压力吗?
会的。背压增大,熔体密度更高,相当于单位体积里含的料更多,会导致填充压力略上升,所以后续要微调保压。
Q:能通过背压解决缩水吗?
可以部分改善,但根本还是靠模具设计(如浇口大小、保压时间)。背压主要是让熔体均匀和致密,减少缩水概率。